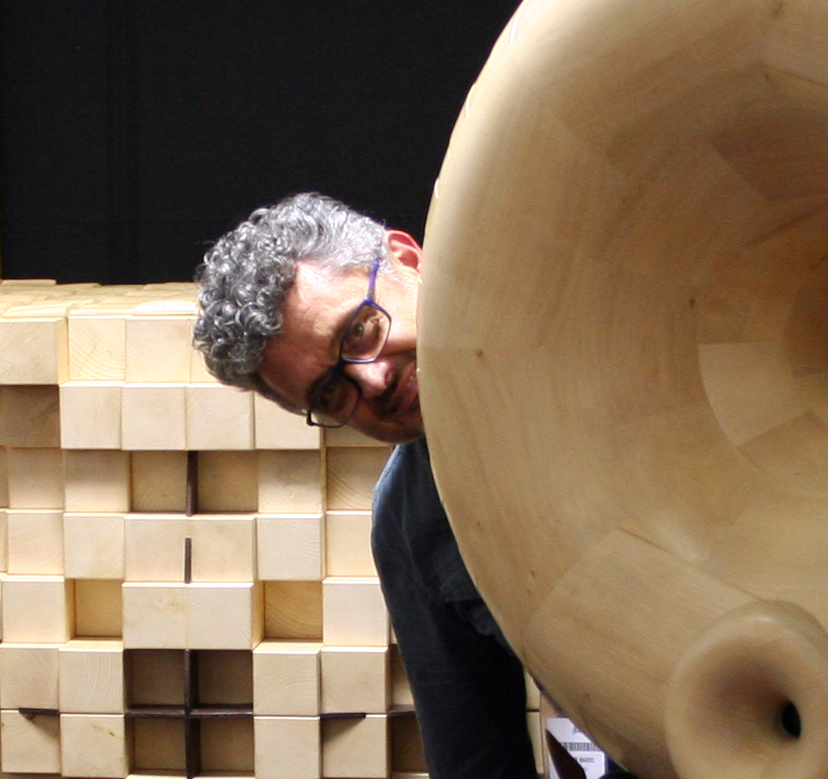
We are specialized in OEM (Original Equipment Manufacturer) and ODM (Original Design Manufacturing) projects. In practice, we offer production services for customers who want their products manufactured according to specific requirements (OEM) or, alternatively, we manage the entire process from design to production (ODM).
Almost all the projects are covered by a stringent NDA.
In the following pages we present some examples.
–> loudspeaker manager for a multi-way high efficiency loudspeaker
–> Xover – EQ – delay – BT 5.0 – 4/6 channels w/ SIGMA STUDIO® interface, battery operated active speaker
© Copyright 2017-2025 CanEVER AUDIO® All rights reserved.
Canever Mario – P. IVA IT04171260278 info@canever.eu